AVIATION TEXTILES - How to manage wearability with Aesthetics
- Rick Roseman
- Aug 7, 2024
- 11 min read
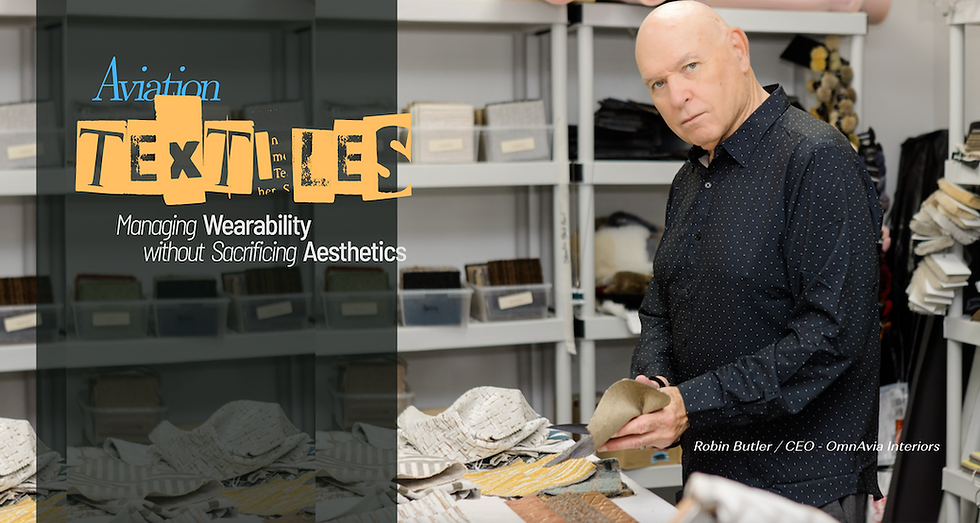
How many times have you selected a fabric that completely floats your boat and that you know your customer will love – only to learn that it’s wearability doesn’t measure up? It's happened to every designer, center and specifier at one time or another. And it’s not something you can afford to just brush aside. The durability profile of a fabric for use on an aircraft, is for better or worse, paramount to aesthetics. In short, if it doesn’t wear…it doesn’t work. But as with most things, knowledge is power and today we have one of the globally acknowledged “Titans of Textiles”, Mr. Robin Butler (OmnAvia Interiors). He’s agreed to answer a few key questions about textiles and in the process give us all a crash course and how to select fabrics with exceptional wearability - without sacrificing the aesthetics we’re all looking for.
RR: So, to start off with I think I understand that a textile refers to the ‘base materials’ that are made from woven fibers - but at what point do textiles become fabrics? I know it’s a basic question but since it’s rather fundamental to our discussion, I thought maybe you could give us a brief explanation.
RB: Great basic question, Rick! Textiles are fibers or yarns that are woven, knitted, entangled or otherwise bonded into flat sheet-like structure. Each construction offers its own set of physical properties (stretch, stiffness, puncture-resistance, abrasion resistance, etc.) to meet the requirements of the fabric’s end use. This is the basis of textile engineering! To me, the real magic in textiles is in the science of fibers – the basic building block of all textile materials. The physical and chemical properties of fibers ultimately determine the properties of the end-product. The fiber’s cross-sectional shape affects light reflection (round creates lustre; irregular means dullness). softness and even moisture wicking performance. Fiber length controls yarn strength, and fiber fineness contributes to both yarn strength and ultimate fabric comfort. Natural animal and plant-based fibers (wool, silk, cotton, viscose rayon, flax, etc.) tend to be water-absorbing (hydrophilic) which improves comfort and dyeability. Most petroleum-based fibers are hydrophobic (moisture-repelling). These can be great for stain-resistance but not as comfortable for apparel use. Petroleum-based synthetic polymer fibers can be engineered to exhibit a variety of physical properties, depending on their ultimate end-use. I find fiber science to be fascinating.

RR: My next question may also seem a little basic for people in aviation, but just so we get the fundamentals out of the way, can you briefly explain how aviation approved fabrics are treated to pass burn and at what level that occurs? Also is it true that flame-retardant chemical coatings are designed to self-extinguish when exposed to flame?
RB: Textiles can be made to be flame-resistant in many ways. Let’s start with treating fibers before they become yarn. Several polymer types are inherently flame-resistant and, when extruded into fibers, these filaments have properties that keep them from igniting except at very high temperatures. These are typically aramids and meta-aramids - Nomex®, Kevlar®, and PBI to name a few. When made into fabrics they are used for fire-protective apparel such as firefighters gear and motorsports drivers’ suits, and cushion fire blocking fabrics. . But they are limited in their range of colors, so they don’t work well in decorative applications.Other synthetic fibers can be made flame-resistant by adding compounds to the molecular chain to make the fiber or yarn inherently flame-resistant. Trevira CS® is an example of a fiber that is commonly used in aviation interiors applications. Fibers such as wool and mohair and some synthetics are frequently treated in the yarn dyeing process, creating a flame-resistant yarn and subsequent fabric with durable flame-resistant properties.
Finally, fabrics are often flame-treated after weaving. The application of either an invisible surface treatment or a back coating that contains an FR additive are an effective means of creating fabrics that meet aviation flammability requirements.
All these treatments are engineered to cause the finished fabric to conform to FAA standards by either self-extinguishing or delaying full ignition long enough to safely escape a survivable incident.
RR: Ok, so with the elemental bits out of the way, let’s move on to more substantive questions. Why is it some fabrics are inherently more durable than others? And also, is there any truth to the notion that highly durable fabric options tend to be less soft or supple to the hand?
RB: There’s no short answer to this question. Generally, the tighter the fabric construction (yarns per square inch), the more durable the fabric. Durability increases when those yarns have longer fiber length and a higher twist. For fun, let’s add the notion that some fibers have a higher tensile strength than others – this makes those fabrics even stronger. But you can have a very durable fabric that is of a coarser weave or knit construction if the fiber type and yarn construction is designed for maximum strength. Fabric finishes (chemical or physical) also can affect a fabric’s durability.
As a general rule, it’s fair to say that the most durable fabrics (think “bullet-proof”) are also those that have the least appealing hand-feel.
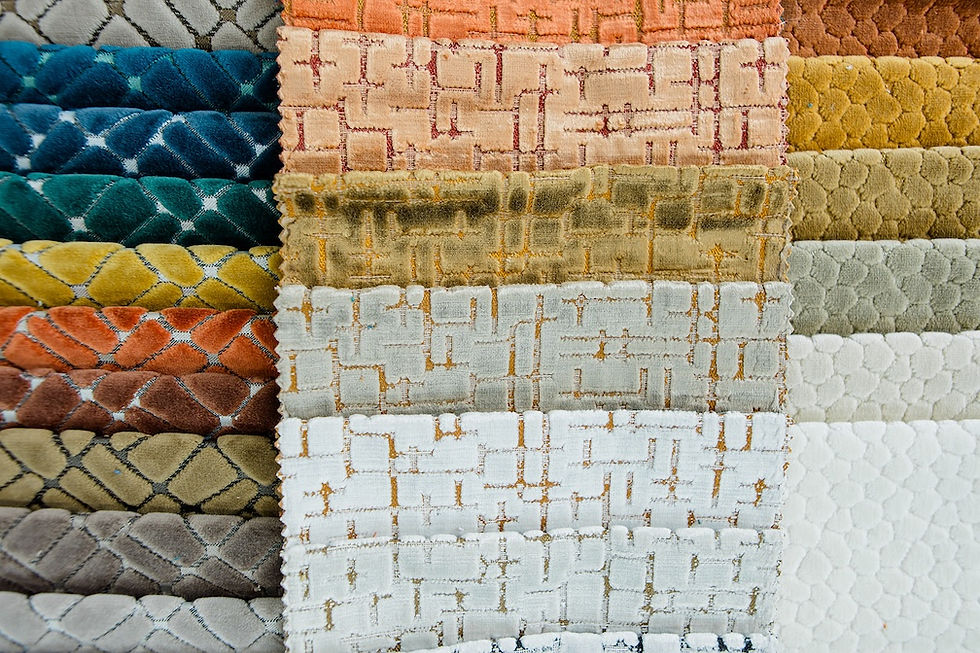
RR: In general, can you tell us what fabrics or textiles tend to be best suited for aviation, and why.
RB: I hope I don’t go too deep into the weeds here, Rick. It’s a complex topic, but this really depends on end-use. First and foremost, aviation fabrics must meet the appropriate flammability standards for their application. Installations that require little to no aesthetics and high flame-resistance call for engineered industrial fabrics such as aramids or PanOx fabrics. Our audience here, however, is more interested in decorative textiles, particularly upholstery for aircraft. For the optimum combination of flame-resistance, tactile appeal and durability, fabrics made from wool and predominately wool/nylon blends perform the best. Wool is inherently flame-resistant, absorbs moisture, and has an excellent hand when the yarn construction and weave are designed properly. The fiber is easily dyeable in a nearly infinite range of colors, and worsted wool yarn lends itself to weave at high speeds (meaning higher output rates and lower costs).
However, many other fibers also make exquisite cabin textiles. These fiber types are polyester, cotton, silk, and rayon, plus even acrylic and nylon (polyamide) in low percentages. Viscose rayon and bamboo silk have a great hand and lustre and are frequently used in carpets as an accent yarn. They replicate silk, but at a much lower cost. Nearly all these fibers can be flame treated to meet specs. Most can be flame treated to meet specs. Olefin (polypropylene) is a poor choice due to its low melting point. When several of these fibers are blended – which create some absolutely exquisite weave pattern, texture and color options - they must be treated with a back coating that contains an FR additive and usually a latex carrier. This type of backing increases the stiffness of the fabric, although it rarely changes the surface color, texture or haptic. For some applications (panel coverings, certain upholstery trims, etc.) the stiffness is not objectionable. For other uses such as curtains, it simply can’t be used.
We recently had a designer who approached us with the challenge to provide a bespoke color of a weave pattern we offered. Her client loved the pattern, but the other cabin elements called for a color variation. Our overseas supplier quickly provided five or six color variations for presentation, and the client made his selection. Weaving the fabric in a short lead time in a small quantity became the next challenge, and again the mill came through. Next, the fabric needed to be flame treated, and it contained a small percentage of acrylic fiber in the blend. The mod center doing the installation was highly skeptical that the fabric would meet oil-burner testing, but our finisher worked his magic and the cushion assemblies passed without a hitch.
Not everything is possible,, but we have confidence in our competence and in the capabilities of our carefully selected vendor base.
RR: Is there any truth to the old stereotype that ‘if it’s beautiful and feels wonderful, it’s probably not durable?’ Has technology been able to change this and deliver fabrics that are truly beautiful and soft to the touch but at the same time, offer great wearability?
RB: Rick, this theory can be debunked with proper fiber selection (wool, silk, fine-denier polyester) and proper fabric design and weave construction. There is not a plethora of these fabrics available today. There are a few mills in the US still weaving wool, and there are mills in Europe and Turkey that are creating stunning fabrics with high abrasion-resistance. They are frequently using modern high-speed jacquard looms or specialized velvet looms to create incredible textures and patterns that are often jaw-dropping. There are also some finishing techniques that allow additional design elements to be applied to the surface of a base weave that create some stunning effects. We’ll soon introduce a limited collection of some of these patterns for the VIP designer who designs for large cabins and is seeking larger scale patterns to bring a “statement” textile to the cabin.
RR: As someone who has spent their entire professional life in textiles and aviation fabrics, can you give us some simple tips to remember when it comes to selecting fabrics that maximize all three of the big concerns: aesthetic, tactile and durability?
RB: Keeping the points in mind that we’ve covered so far – fiber selection, weave integrity, flame-resistance that can be verified by a DER. It’s important for peace of mind to source from a supplier who understands FAA/EASA flammability requirements, will stand behind their performance claims, and can use their resources to provide that hard-to-find fabric.
RR: Lastly Robin, can you please tell us what types of fabrics are most commonly used for seating upholstery these days – and if perhaps there are any new weaves that are trending at the moment?
RB: Trends are more for color and texture in fabrics today. The color palette has been in greys in recent years, but as in all fashion, trends change and we see some movement back to neutrals of late. We have introduced a few new fabrics constructed of epengle velvet’ jacquard weaves, as well as a flat-woven series of panel fabrics (Fortezza) that are visually textural and are high-performance. We constantly seek new and interesting fabrics for our clients. Textiles are my passion, and have been since my studies at the Wilson College of Textiles at NC State University. I want in some small way to share that passion with this marvelous industry that we are all a part of.
Thank you Robin. We greatly appreciate your time and expertise. I know my questions must all be very fundamental in your world, but I think many of our readers will benefit from your explanations and perhaps alleviate some of the grappling the next time they head to the design centers.
RR: Ok, so with the elemental bits out of the way, let’s move on to more substantive questions. Why is it some fabrics are inherently more durable than others? And also, is there any truth to the notion that highly durable fabric options tend to be less soft or supple to the hand?
RB: There’s no short answer to this question. Generally, the tighter the fabric construction (yarns per square inch), the more durable the fabric. Durability increases when those yarns have longer fiber length and a higher twist. For fun, let’s add the notion that some fibers have a higher tensile strength than others – this makes those fabrics even stronger. But you can have a very durable fabric that is of a coarser weave or knit construction if the fiber type and yarn construction is designed for maximum strength. Fabric finishes (chemical or physical) also can affect a fabric’s durability.
As a general rule, it’s fair to say that the most durable fabrics (think “bullet-proof”) are also those that have the least appealing hand-feel.
RR: In general, can you tell us what fabrics or textiles tend to be best suited for aviation, and why.
RB: I hope I don’t go too deep into the weeds here, Rick. It’s a complex topic, but this really depends on end-use. First and foremost, aviation fabrics must meet the appropriate flammability standards for their application. Installations that require little to no aesthetics and high flame-resistance call for engineered industrial fabrics such as aramids or PanOx fabrics. Our audience here, however, is more interested in decorative textiles, particularly upholstery for aircraft. For the optimum combination of flame-resistance, tactile appeal and durability, fabrics made from wool and predominately wool/nylon blends perform the best. Wool is inherently flame-resistant, absorbs moisture, and has an excellent hand when the yarn construction and weave are designed properly. The fiber is easily dyeable in a nearly infinite range of colors, and worsted wool yarn lends itself to weave at high speeds (meaning higher output rates and lower costs).
However, many other fibers also make exquisite cabin textiles. These fiber types are polyester, cotton, silk, and rayon, plus even acrylic and nylon (polyamide) in low percentages. Viscose rayon and bamboo silk have a great hand and lustre and are frequently used in carpets as an accent yarn. They replicate silk, but at a much lower cost. Nearly all these fibers can be flame treated to meet specs. Most can be flame treated to meet specs. Olefin (polypropylene) is a poor choice due to its low melting point. When several of these fibers are blended – which create some absolutely exquisite weave pattern, texture and color options - they must be treated with a back coating that contains an FR additive and usually a latex carrier. This type of backing increases the stiffness of the fabric, although it rarely changes the surface color, texture or haptic. For some applications (panel coverings, certain upholstery trims, etc.) the stiffness is not objectionable. For other uses such as curtains, it simply can’t be used.
We recently had a designer who approached us with the challenge to provide a bespoke color of a weave pattern we offered. Her client loved the pattern, but the other cabin elements called for a color variation. Our overseas supplier quickly provided five or six color variations for presentation, and the client made his selection. Weaving the fabric in a short lead time in a small quantity became the next challenge, and again the mill came through. Next, the fabric needed to be flame treated, and it contained a small percentage of acrylic fiber in the blend. The mod center doing the installation was highly skeptical that the fabric would meet oil-burner testing, but our finisher worked his magic and the cushion assemblies passed without a hitch.
Not everything is possible,, but we have confidence in our competence and in the capabilities of our carefully selected vendor base.
RR: Is there any truth to the old stereotype that ‘if it’s beautiful and feels wonderful, it’s probably not durable?’ Has technology been able to change this and deliver fabrics that are truly beautiful and soft to the touch but at the same time, offer great wearability?
RB: Rick, this theory can be debunked with proper fiber selection (wool, silk, fine-denier polyester) and proper fabric design and weave construction. There is not a plethora of these fabrics available today. There are a few mills in the US still weaving wool, and there are mills in Europe and Turkey that are creating stunning fabrics with high abrasion-resistance. They are frequently using modern high-speed jacquard looms or specialized velvet looms to create incredible textures and patterns that are often jaw-dropping. There are also some finishing techniques that allow additional design elements to be applied to the surface of a base weave that create some stunning effects. We’ll soon introduce a limited collection of some of these patterns for the VIP designer who designs for large cabins and is seeking larger scale patterns to bring a “statement” textile to the cabin.
RR: As someone who has spent their entire professional life in textiles and aviation fabrics, can you give us some simple tips to remember when it comes to selecting fabrics that maximize all three of the big concerns: aesthetic, tactile and durability?
RB: Keeping the points in mind that we’ve covered so far – fiber selection, weave integrity, flame-resistance that can be verified by a DER. It’s important for peace of mind to source from a supplier who understands FAA/EASA flammability requirements, will stand behind their performance claims, and can use their resources to provide that hard-to-find fabric.
RR: Lastly Robin, can you please tell us what types of fabrics are most commonly used for seating upholstery these days – and if perhaps there are any new weaves that are trending at the moment?
RB: Trends are more for color and texture in fabrics today. The color palette has been in greys in recent years, but as in all fashion, trends change and we see some movement back to neutrals of late. We have introduced a few new fabrics constructed of epengle velvet’ jacquard weaves, as well as a flat-woven series of panel fabrics (Fortezza) that are visually textural and are high-performance. We constantly seek new and interesting fabrics for our clients. Textiles are my passion, and have been since my studies at the Wilson College of Textiles at NC State University. I want in some small way to share that passion with this marvelous industry that we are all a part of.
Thank you Robin. We greatly appreciate your time and expertise. I know my questions must all be very fundamental in your world, but I think many of our readers will benefit from your explanations and perhaps alleviate some of the grappling the next time they head to the design centers.
For more on Robin Butler and OmnAvia Interiors, visit:
Visit: omnaviainteriors.com
Comments